详细介绍:
大型回转支承机加工工艺及刀具在回转支承风电轴承的应用
大型回转支承又称转盘轴承或特大型轴承,是一种能够承受综合载荷的大型轴承,可以同时承受较大的径向载荷、轴向载荷和倾翻力矩,转盘轴承广泛用于起重运输机械、港口机械、船舶机具以及其它方面的大型回转装置上。
由于大型回转支承体积大,零件截面积小,加工精度高,工序长,易变形,因此加工的难度增大,我们对回转支承的各部支承环、外圈采取了相应的工艺措施,并按照设计要求加工出来,经装配试车和一年多的使用检验,完全满足了原设计要求,有些方面甚至高于原设计要求。
1, 毛坯锻制的选择
回转支承的大型加工件有三件支承环、外圈、固定环。由于支撑环和固定环属薄壁的环形零件,若单件毛片锻制是需要毛坯余量较大,同时为防止热处理变形,调制余量也需增大。由于固定环和支撑环内外圆尺寸比较近似,经过反复分析,锻制大型锻件比较容易,将固定环与支撑环锻打为一体,这样一套回转支承其毛坯锻件为两件,一件外圈,另一件为固定环和支撑环的合锻件。
2, 淬火处理
由于固定环、支承环要求淬硬层为3-5mm 表面淬火后硬度达到HRC55-60.该零件直径尺寸较大,但截面积尺寸较小,精车到量后再表面淬火,变形量如果超差,那就只能报废,损失大。如先淬火,则淬硬层厚度应为留量加上3-5mm,如留量小于变形量,则造成废品,若留量大于变形量,则难加工。经过计算确定,半精加工时,淬火面滚道面留量2mm,淬硬层厚为5-7mm,如果在淬火时多点支承,则变形量小与1.5mm.
精加工
在车削过程中,由于其硬度基本为HRC59-60 所以先用我们研制的特种合金刀具并采取低速小进给进行车削,待留量为0.02mm时,再用砂轮进行磨削至尺寸要求时,以达到尺寸粗糙度要求与图纸技术要求,为制造优质的回转支承奠定了基础。
华菱BN-S20立方氮化硼刀片在回转支承、风电转盘轴承行业的应用
回转支承/风电转盘轴承套圈表面淬火后硬度达到HRC55~62,淬硬层一般为3~5mm, 50Mn或42CrMo材质回转支承、风电转盘轴承套圈以车代磨常用立车进行干式切削加工;回转支承环硬车削工序因为加工余量大而且滚道和轴承面在淬火后加工(硬车)时加工精度要求严格,对硬车刀片的韧性和耐磨性提出了很大的挑战。超硬硬车刀片的性能平衡成为回转支承、风电转盘轴承以车代磨工艺的关键步骤。立方氮化硼刀片是目前黑色金属加工用刀具中最硬的刀具材质,作为热后硬车刀片已经广为熟知,由于脆性的限制,一般限于淬火后小余量以车代磨使用;根据回转支承、风电转盘轴承行业硬车加工余量大的特性,探讨此行业以车代磨工艺以及硬车用超硬刀具的发展。
回转支承、风电转盘轴承硬车加工对刀具性能的要求
回转支承、风电转盘轴承的热后硬车工序的加工余量是根据此前的热处理工艺及淬火变形量预留的,一般回转回转支承、风电转盘轴承淬火后硬车余量为2—6mm;硬车刀片在大余量加工淬火后的回转支承、风电转盘轴承内外圈时需要优异抗冲击韧性;可见回转支承内外环淬火后硬车难点在立方氮化硼刀片韧性要求高,而回转支承滚道热后精车光洁度要求及尺寸稳定性要求立方氮化硼刀片耐磨性能和热稳定性优异。所以回转支承转盘轴承行业要么抱怨立方氮化硼刀片硬度低不耐磨造成加工光洁度差,要么是刀片太脆易崩刀,特别是断续面切削部位。
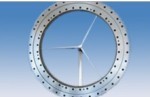
针对回转支承、风电转盘轴承硬车加工对立方氮化硼刀片的性能要求,华菱超硬研制出非金属粘合剂立方氮化硼刀片BN-S20牌号, 作为国内唯一一家非金属基结合剂超硬刀具,BN-S20牌号保证了立方氮化硼刀具韧性的同时,避免了因加入金属结合剂而导致CBN刀具受热后金属结合剂过早软化造成的刀片寿命降低, BN-S20牌号适合对大型淬火后高硬度工件进行中高速粗精车,其硬度为HRC98.5;可加工热处理后硬度范围:HRC45--HRC79。适合长时间大余量硬态车削或以车代磨。
以车代磨工艺在回转支承/风电转盘轴承行业的可行性及新牌号CBN刀具的使用案例:
案例一:以BN-S20牌号超硬刀片加工风电转盘轴承套圈为例,淬火后精车余量5mm;线速度90-150m/min淬火后精车粗糙度沟道表面粗糙度达到Ra0.3μm,满足以车代磨工艺要求;热后硬车双桃形沟道的沟底跳动全部<0.005mm,从加工效率和成本考虑,以车代磨优势明显,以轴承行业加工风电1.5MW机组用变浆轴承内外圈(尺寸:外径φ1900mm,厚130mm)为例,如果淬火后加工余量全部采用磨削加工,磨时间是18小时以上,采用以车代磨工艺,时间只需4.5小时。在同样加工精度的要求下,采用车加工效率是磨加工的4倍;从刀具耐用度来讲,BN-S20牌号立方氮化硼刀片车削1900风电变浆轴承套圈为例,可精车30多件套圈;所消耗的电能及人工,物料耗材却只有磨削的1/5;刀具耐用度高,使用成本更低。
案例二:淬火后硬车50Mn材质大型回转支承外环,热处理后硬度HRC55,单边加工余量2.5mm。因50Mn环件淬火后的变形,内孔呈不规整圆形,原用超硬刀片经常出现崩刃现象,为了降低刀具的崩损损耗,只能采用多次走刀加工完成,导致加工效率低,设备占有率高,电费、辅助材料费用等综合加工成本增加。采用非金属粘合剂BN-S20牌号超硬刀片,切削深度2.5mm左右,不规整处达到3mm;采用一次走刀加工完成,减少走刀次数加工效率提高3倍,刀片并不是令人担心的崩刀、碎裂;且因非金属粘合剂热导率高,在相同转速下,比原常见金属粘合剂整体超硬刀片寿命高出50%。 BN-S20材质C超硬刀片相比普通超硬刀片,制造成本只增加了10%,但换来的是3倍的加工效率提升和1.5倍的刀具寿命,用户的刀具使用成本大幅度降低。
用以车代磨工艺对热后回转支承、风电转盘轴承内外圈硬车加工时,与磨削相比,避免了磨削烧伤,而且,硬车削大型轴承可选择干式切削方式,经济环保;而且相比磨削加工,硬车削下来的铁屑可以很方便处理,作为资源回收利用成本低,减少对环境污染。
以车代磨工艺的风险及控制
硬车所用机床间隙和刚性决定了震刀、让刀问题的发生几率,亦会影响加工工件的尺寸精度和表面粗糙度,所以需要根据自身工件的要求及现用设备状况针对性的选择刀片的几何形状包括立方氮化硼刀片刃口的微观处理,以最大程度降低以车代磨工艺风险。
针对回转支承、风电转盘轴承行业以车代磨,常用刀片几何尺寸型号根据转盘轴承型号和工艺选择;一般内外圈部位加工常用立方氮化硼刀片材质牌号BN-S20;它不但适合大直径回转支承和风电转盘轴承,也适合非标轴承以车代磨,直径500mm以下整体淬火硬度HRC60以上轴承套圈的大余量一次走刀代替粗磨工序;对于淬火后加工余量小于0.3mm的小尺寸轴承套圈可选用BN-H20牌号立方氮化硼.
需要注意的是对淬火后轴承套圈硬车削余量较大或有断续加工时刀片需刃口处理0.2*20度负倒棱,且配套车刀杆设计出装卡负前角6-7度为佳;小余量热后精车时刀片刃口处理一般取0.1mm负倒棱;刀片刀尖圆弧半径根据轴承套圈车加工所用工装夹具进行选择,以确保整个以车代磨加工过程不振刀,不让刀。
大型回转支承机加工工艺及刀具在回转支承风电轴承的应用
|